-
Based on Linux+Xenomai Real-time Environment Construction
It adopts the strong real-time extension of the Linux kernel with dual-core mechanism. It provides rich functions for the development of strong real-time applications and a reliable operating environment for robot motion planning. The Atomrobot control system is developed based on the ROS+OROCOS platform and is the only control system dedicated to parallel robots in China.
-
Control system based on ROS+OROCOS platform
Based on the ROS platform, the robot control system integrates event-driven architecture and layered architecture. The modules for robot control and operation application processing, such as the visual system, robot motion control center, and human-machine interaction interface, use ROS topics and services for communication. The module deployment and interaction coupling are low, and it is easy to develop and maintain. Similarly, ROS encapsulates the robot's hardware. Different robots and different sensors can be represented in the same way in ROS (topic, etc.) for upper-level applications (motion planning, etc.) to call.
-
Acontis-based Ethercat communication stack
The real-time industrial fieldbus communication protocol based on the Ethernet development framework is one of the fastest industrial Ethernet technologies, providing nanosecond-level precise synchronization. It has the characteristics of high performance, flexible topology, easy application, low cost, and high-precision equipment synchronization.
Core Technology
-
Multi-robot
Model SupportIn addition to classic parallel configurations such as 2-axis, 3-axis, and 3+1, it also supports 5-axis and 6-axis serial-parallel mixed models and stewart platforms.
-
Complex Trajectory
MemoryBy fitting the trajectory with a spline curve, memory tracking of complex teaching trajectories can be achieved.
-
Speed Look-ahead
Through speed look-ahead technology, a smoother speed curve can be obtained. Even in situations where the acceleration changes frequently, a smoother speed curve can still be obtained, thereby improving the operation efficiency of the robot.
-
Drap Teaching
By directly holding and pulling the robot, the posture data of the teaching process can be recorded, and the robot application tasks can be taught in an intuitive way.
-
Vibration Suppression
The vibration suppression algorithm can effectively reduce the mechanical vibration caused by the robot's high-speed sudden stop, thereby improving the positioning accuracy of the robot under high-speed operation.
-
Multi-axis Linkage
In addition to the main body, multiple external servo axes can also be controlled to perform multi-axis linkage independently or synchronously with the robot.
-
Dynamic Tracking
With the support of robot vision or encoders, objects moving along straight lines or arcs can be grasped and released in a follow-up manner.
-
Paletizing
Provides palletizing algorithm, inputs palletizing configuration to automatically generate motion trajectory to improve efficiency.
-
IoT Module
Connect the IoT module and remotely observe the current operating status of the device via your mobile phone.
-
SoftPLC
Soft PLC是除了通过在Hmi界面输入命令之外,与用户交互的另外一个接口。用户通过Soft PLC可以进行PLC编程,管理和控制控制器上连接的IO。
-
Disc Tracking
The object information is obtained through vision, and a motion relationship is established between the robot and the disc conveyor belt to track the motion trajectory of the object on the disc in real time.
-
Regional Monitoring
By setting the working area and prohibited area to avoid unexpected situations such as collisions, the control system will monitor the robot's working space in real time, and control the start and stop of the manipulator based on the relationship between the monitoring areas.
Vision System
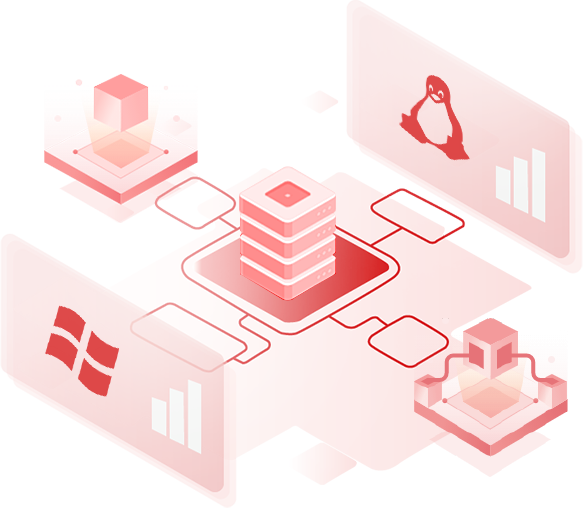
Cross-platform Vision System
Supports cross-platform applications of Windows/Linux, and can realize the deployment of visual applications on different platforms.
Multiple Target Recognition Algorithms
Supports multiple detection methods such as Blob, template matching, character QR code recognition, and workpiece positioning.
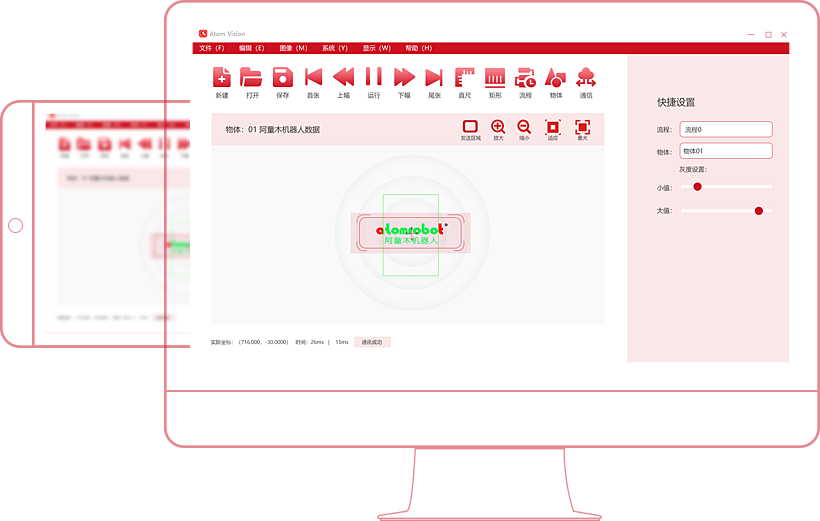
Simple and Fast User Interface Operation
According to user habits, we develop quick operation interfaces for grayscale and object flow. At the same time, we provide functions for user operation such as camera angle, pixel ratio calculation, 9-point teaching, and multi-client/server support.